¿Qué es un sistema de MRP?
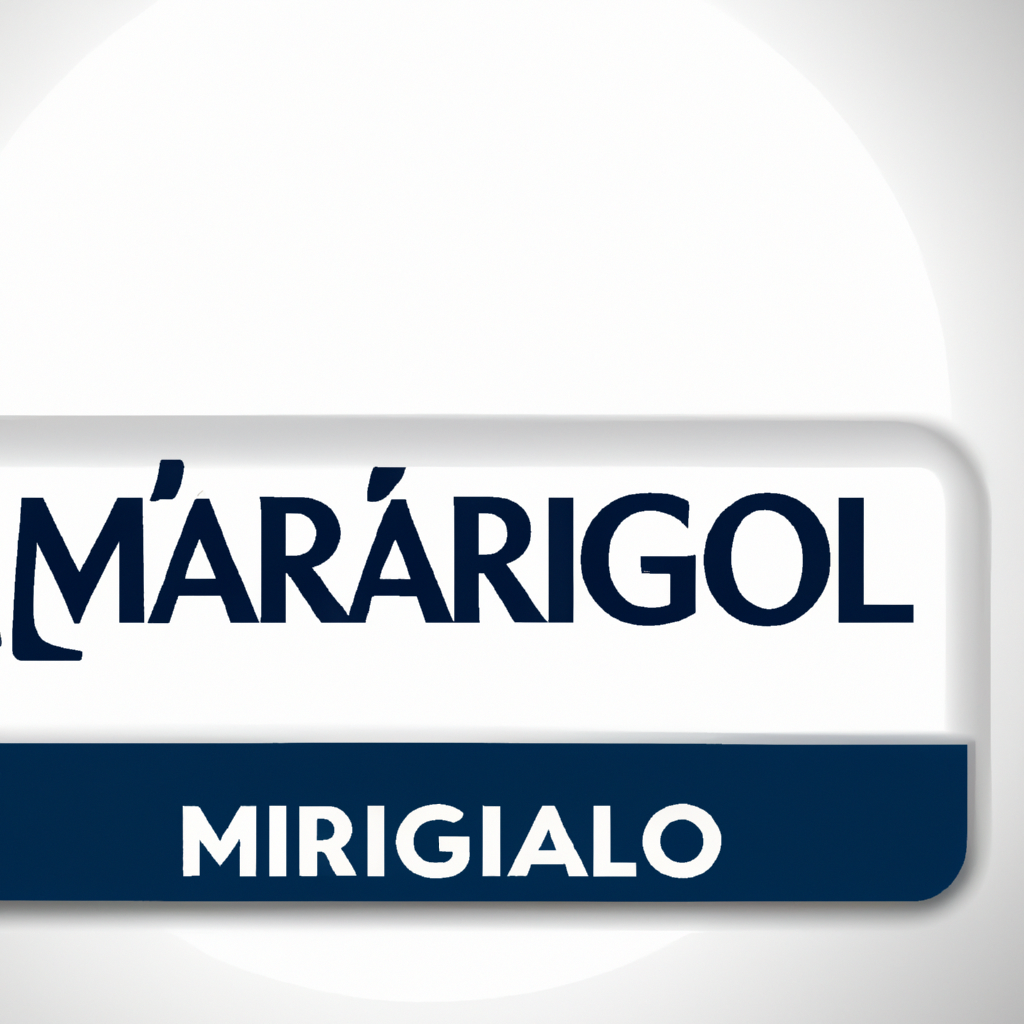
Un sistema de MRP (Material Requirements Planning, por sus siglas en inglés) es una herramienta de gestión utilizada en el ámbito de la producción y logística para planificar y controlar los recursos necesarios para la fabricación de productos.
El sistema de MRP se basa en la generación de programaciones de producción a partir de la demanda prevista, teniendo en cuenta los niveles de inventario, los tiempos de producción y los plazos de entrega de los proveedores.
El objetivo principal de un sistema de MRP es optimizar la gestión de los recursos, evitando faltantes o excesos de inventario, reduciendo costos y mejorando la eficiencia en la producción.
Para ello, el sistema de MRP utiliza la información sobre la planificación de la demanda, los tiempos de producción, las capacidades de las máquinas, los niveles de inventario, los plazos de entrega y las órdenes de compra o producción, entre otros datos relevantes.
En base a esta información, el sistema de MRP genera programas de producción detallados, indicando qué productos o componentes deben fabricarse, en qué cantidad y en qué momento, así como los recursos necesarios y las fechas de entrega.
De esta manera, el sistema de MRP permite evitar faltantes o excesos de inventario, planificar adecuadamente la producción, minimizar los tiempos de espera y mejorar la calidad del servicio al cliente.
En resumen, un sistema de MRP es una herramienta de gestión que permite planificar y controlar los recursos necesarios para la fabricación de productos, optimizando la gestión de inventarios y la eficiencia en la producción.
¿Qué es el sistema de MRP?
El sistema de MRP, también conocido como Planificación de Requerimientos de Materiales por sus siglas en inglés, es una herramienta que permite gestionar y controlar eficientemente los materiales necesarios para la producción de bienes y servicios.
El sistema de MRP tiene como principal objetivo optimizar la gestión de inventarios, evitando sobrecostos y excesos de stock, al mismo tiempo que garantiza la disponibilidad de los materiales necesarios en el momento y cantidad adecuada.
El sistema de MRP se basa en una serie de cálculos y registros de información que permiten planificar las compras y la producción de manera eficiente. Utiliza información como la demanda de los productos, el tiempo de entrega de los proveedores, el ciclo de vida del producto y los niveles de inventario, entre otros, para determinar las cantidades y tiempos de adquisición de los materiales necesarios.
Una de las principales ventajas del sistema de MRP es que permite reducir los costos de almacenamiento y los riesgos de quedarse sin stock. Esto se logra al optimizar los procesos de compra y producción, evitando excedentes o faltantes que puedan afectar la cadena de suministro y la satisfacción del cliente.
Además, el sistema de MRP ayuda a establecer cronogramas de producción, distribución y entrega de productos más precisos, lo que contribuye a optimizar la planificación de la producción y la logística.
En resumen, el sistema de MRP es una herramienta clave para la gestión eficiente de los materiales necesarios en la producción. Permite controlar los inventarios, optimizar las compras y producciones, y garantizar la disponibilidad de los materiales en los momentos y cantidades adecuadas. Su uso adecuado puede ser fundamental para lograr una gestión eficiente de la cadena de suministro y mejorar la rentabilidad de las empresas.
¿Qué es un MRP ejemplo?
Un MRP ejemplo se refiere a un sistema de planificación de recursos materiales que ayuda a las empresas a administrar eficientemente sus inventarios y la producción. MRP es la sigla de Material Requirements Planning, que en español se traduce como Planificación de los Requerimientos de Materiales.
El objetivo principal de un MRP ejemplo es garantizar que una empresa tenga los materiales adecuados en el momento adecuado y en la cantidad adecuada. Esto se logra mediante el procesamiento de información sobre las órdenes de producción, los niveles de inventario actual y los plazos de entrega de los proveedores.
Por ejemplo, si una empresa fabrica automóviles, el MRP ejemplo calculará la cantidad de cada componente necesario para ensamblar un automóvil, teniendo en cuenta la demanda prevista y los inventarios actuales. Esto permite a la empresa realizar pedidos a los proveedores con anticipación, evitando así problemas de falta de stock.
El MRP ejemplo también tiene en cuenta otros factores, como el tiempo de producción, la capacidad de la planta y los plazos de entrega de los proveedores. De esta manera, ayuda a la empresa a diseñar un plan de producción eficiente y minimizar los costos de almacenamiento y el riesgo de quedarse sin materiales.
En resumen, un MRP ejemplo es una herramienta invaluable para las empresas que desean optimizar su cadena de suministro y asegurarse de tener los materiales necesarios para cumplir con la demanda de sus productos. Al utilizar un sistema MRP, las empresas pueden mejorar su eficiencia, reducir costos y garantizar la satisfacción de sus clientes.
¿Qué es un sistema de MRP y ERP?
Un sistema de MRP (Material Requirements Planning) y ERP (Enterprise Resource Planning) son dos herramientas clave que se utilizan en el ámbito empresarial para gestionar eficientemente los recursos y planificar las necesidades de una organización. El MRP es un sistema que se encarga de administrar y controlar el inventario de materiales necesarios para la producción, teniendo en cuenta la demanda, la disponibilidad de los recursos y los tiempos de entrega. De esta forma, permite optimizar el proceso de producción, evitando escasez o exceso de stock y maximizando la eficiencia operativa. Por otro lado, el ERP es una herramienta más amplia que integra todos los procesos y departamentos de una organización, incluyendo la gestión de recursos humanos, finanzas, compras, ventas, logística, entre otros. Este sistema utiliza una base de datos centralizada que permite a los diferentes departamentos compartir información en tiempo real, evitando duplicidades y mejorando la toma de decisiones. Ambos sistemas son fundamentales en la gestión de una empresa, ya que permiten una visión global de los recursos disponibles, facilitando la planificación y programación de las operaciones. Además, ambos sistemas brindan información precisa y actualizada, lo que ayuda a mejorar la eficiencia en la cadena de suministro y reducir los costos operativos. En resumen, un sistema de MRP se enfoca en la gestión del inventario y la planificación de la producción, mientras que un sistema de ERP va más allá e integra todos los procesos de la organización. Estas herramientas son indispensables para mejorar la productividad, optimizar los recursos y tener un mayor control sobre las operaciones de la empresa.
¿Qué tipos de MRP hay?
El MRP (Material Requirements Planning) es un sistema de planificación y control que se utiliza en la gestión de inventarios.
Existen distintos tipos de MRP que se adaptan a las necesidades de cada empresa.
El MRP básico es el que se encarga de calcular las cantidades de materiales necesarios para cumplir con la demanda de producción. Utiliza los datos de los pedidos de los clientes, los niveles de inventario y los tiempos de producción para determinar cuánto y cuándo se deben comprar o producir los materiales.
Otro tipo de MRP es el MRP II (Manufacturing Resource Planning).
Este sistema va más allá del cálculo de las necesidades de materiales y también considera otros recursos necesarios para la producción, como la capacidad de producción, los recursos humanos y las máquinas. El objetivo del MRP II es planificar y programar todos los recursos de la empresa de manera eficiente, asegurando que están disponibles en el momento adecuado y en las cantidades necesarias.
El MRP II también incluye la gestión de órdenes de compra, la programación de la producción y el control de calidad, entre otras funciones.
Otro tipo de MRP es el MRP III (Manufacturing Resource Planning III).
Este sistema va aún más allá que el MRP II y se enfoca en la gestión integrada de la cadena de suministro. El MRP III busca optimizar todos los procesos relacionados con la producción y el abastecimiento, desde la adquisición de materiales hasta la entrega del producto final al cliente.
Además, el MRP III también suele incluir la gestión de la demanda, la gestión de inventario, la gestión de operaciones y la gestión de proyectos.
En resumen, existen diferentes tipos de MRP que van desde el cálculo de las necesidades de materiales hasta la gestión integrada de la cadena de suministro. Cada tipo de MRP tiene sus ventajas y se adapta a diferentes niveles de complejidad y necesidades de gestión en las empresas.